About TSUDAKOMA
- HOME
- About TSUDAKOMA
- The Manufacturing Spirit
The Manufacturing Spirit
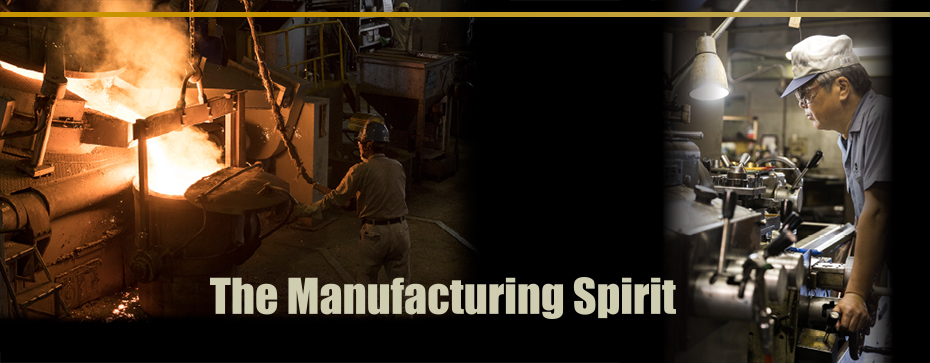
The world's fastest jet loom
The birth of a legend
A new legend was born in Milan, Italy, on November 12, 2015. The fastest ever jet-loom speed of 2,105 rpm was achieved.
At a trade show held in Milan, TSUDAKOMA's Concept Model Air Jet Loom demonstrated stable operation at a speed of 2,105 rpm, which is the fastest ever for a jet loom, for the prescribed demonstration time of 20 minutes. The figure "2,105 rpm" means that 2,105 weft threads are inserted per one minute.
During the 8-day period of the trade show, 8 demonstrations were given with this model every day without experiencing any trouble. Our booth was packed with many visitors who came to see the world's fastest ever jet loom. Everyone was excited and some visitors even took pictures.
Technological integration within the company
In the past, we successfully gave a demonstration at a speed of 1,950 rpm at an international trade show. But like all other manufacturers, stable operation at a speed higher than 2,000 rpm was a great challenge that couldn't be overcome. We developed a variety of new mechanisms and technologies in order to overcome this challenge. One such project was to reduce the weight of moving components by developing components made of Carbon Fiber Reinforced Plastic (CFRP). This project was possible because of our skills and technology regarding composite machinery. Through internal collaboration between the weaving machine development section and the composite machinery section, we developed weaving machine components made of CFRP for sections that move at high speed and sections that require sensitive movements. We solved the two challenges of weaving machine development, to reduce machine weight and to secure strength, with carbon fiber composite machinery that had been developed by applying weaving machine technologies.
It was a significant first step for the development of high-speed weaving machines.
Successful development of rotary tables
Beginning the development of machine tools during WWII
Our machine tool device business was launched back in 1937. Once Japan began to be ruled by a wartime regime, importing foreign-made machine tools was prohibited. At the same time, many domestic machine manufacturers were designated as arms factories. For the purpose of manufacturing military equipment and supplies, TSUDAKOMA and other prominent manufacturers of the region began to develop machine tools, which was an untapped field in Japan at the time. Through its efforts to develop and manufacture lathes and other machine tools, TSUDAKOMA found its own unique path in the development of machine vises and high-precision indexers for milling machines.
Venturing into the unknown: the challenge to develop indexers
Although many domestic machine tool manufacturers achieved growth and development in the following years, none of them were manufacturing indexers as attachments. TSUDAKOMA daringly decided to focus on this field. Development activities started from disassembling imported indexers and sketching the components. Indeed, they started from zero.
Their activities must have been very similar to that of Yonejiro Tsuda when he was studying weaving machines by thoroughly observing and sketching foreign-made weaving machines installed in a nearby textile manufacturer.
The largest market share for NC rotary tables
TSUDAKOMA's successful development of a clamping sleeve method and a special double lead worm gear system in 1984 gave the company the impetus to start leading other manufacturers in the field of numerically controlled rotary tables, a high-accuracy indexing device. These systems were developed to reduce maintenance work to the greatest extent possible and minimize accuracy problems due to backlash, i.e., unsmooth meshing of gears, and wear. It is with these systems that TSUDAKOMA grew into a company that holds the largest market share for NC rotary tables in Japan.
The world's first BallDrive® NC rotary table
We started selling the world's first BallDrive® NC rotary table at full scale in 2016. This was the first product in the world that employed a power transmission method using gears and steel balls instead of the conventional method based on meshing gears. An NC rotary table using this method has no backlash due to its mechanism and does not require braking by clamps. Since this product features ultra-high accuracy and dramatically reduces the time required for machining items with an NC rotary table, it has been adopted and highly rated by many domestic automotive manufacturers that pursue accuracy and production efficiency.
The birth of composite machinery
An encounter through a keyword search
It all began when an employee of a large domestic aircraft manufacturer did a keyword search in 2007 with the following two terms: "fiber" and "machine tools." This initiated the development of Japan's first automatic lay-up machine for carbon fiber composite materials.
Foreign-made lay-up machines for such materials already existed at that time, but the employee's company was not happy with those products in terms of maintenance and after-sales services. They were looking for a domestic manufacturer that could develop such machines and our company's name came up when the employee did a keyword search on the Internet. After obtaining this result, they immediately contacted us.
Technologies nurtured over the years generate cutting-edge technology
In order to create thick components using ultra-thin 0.4 mm-thick carbon fiber sheets, a large number of those thin sheets must be laid up while placing each sheet at the correct position and precisely changing the positioning angle. Technologies for precise tension control and positioning were essential for automating this lay-up process that had conventionally been performed by hand. Although we were new to automatic lay-up, precise tension control and positioning were the two technologies that we had been developing for years for our textile machines and machine tool attachments. "There is no doubt we can develop automatic lay-up machines!" With this confidence and belief, our engineers succeeded in commercializing an automatic lay-up machine in one and a half year since we were first contacted by the aircraft manufacturer.
From the field of aircrafts to the fields of automobiles and industrial machinery
Successfully developed as described so far, Japan's first system for carbon fiber composite materials consisting of an automatic lay-up machine, a slitter, and a drape forming machine, was delivered to a large domestic manufacturer in the heavy industries and has been used for manufacturing components for new aircraft models. While it is known that passing the quality inspections of aircraft manufacturers is extremely difficult and that many modifications must be made before your product is certified, our lay-up machine passed this inspection the first time around. The aircraft manufacturer accepted the lay-up machine with astonishment. So far we have delivered three sets of this system. The machines were modified for each new delivery since there has been a constant request to evolve them. Our engineers have also been growing continuously through this project.
Meanwhile, in addition to the aircraft industry, there are many promising potential uses of carbon fiber materials in the automotive industry. We have already been developing machines jointly with automotive manufacturers and have identified certain directions for the development. At the stage of dissemination and mass-production of carbon fiber materials, automation of the lay-up process is essential. TSUDAKOMA's technologies will do doubt be leveraged by many more manufacturers in the very near future.
Contact Us
For catalogs, drawings, and any inquiries, contact us by contact form.